MSE Team takes top honors in I AM Hydro challenge
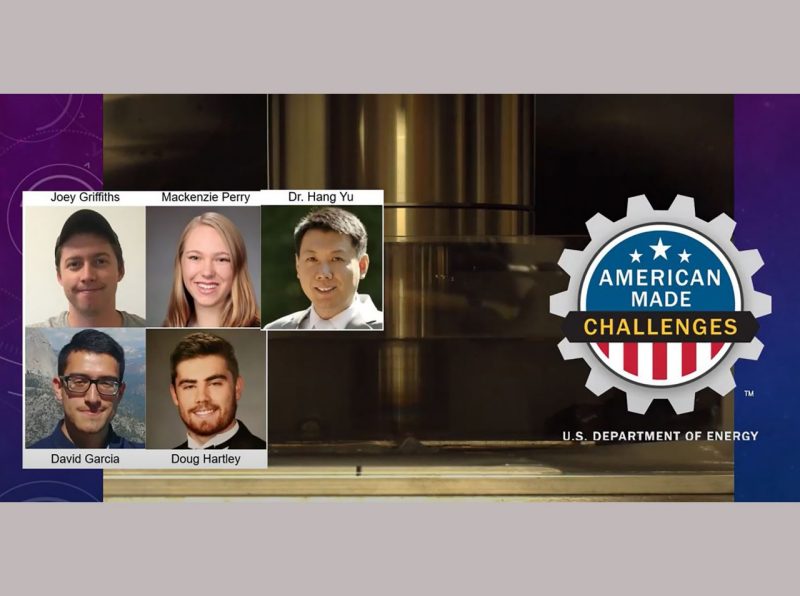
A field of 42 teams (totaling 470 members) from across the United States had 120 days to meet the challenge to “dramatically lower costs and/or improve performance of hydropower components” through the application of advanced manufacturing technologies and advanced materials. The competition, dubbed Innovations in Advanced Manufacturing for Hydropower (I AM Hydro), was sponsored by the U.S. DOE Water Power Technologies Office with a cash prize pot of $175,000.
According to Virginia Tech’s Materials Science and Engineering team, named Fusion-Free Fabrication, “Hydroelectric power is a reliable, renewable energy source that provides electricity to millions of American homes and businesses every year.” Initial capital investment and operation and maintenance (O&M) costs for hydroelectric power are some of the highest costs among the sources of renewable energy (e.g., solar and wind). Thus, there is strong motivation to extend component lifetime through rehabilitation and reduced O&M costs.
Some of the more critical components in hydropower plants are the turbine runners, which operate under water and are subject to corrosion, erosion, cavitation, and fatigue cracking. The MSE report further states, “Current repair strategies involve dewatering the facility, manual inspection, building a scaffold up to the turbine, grinding down damaged surfaces, using arc-welding variants to replace lost material, and post-process grinding to achieve proper dimensions.”
The Fusion-Free Fabrication team “uses an emergent solid-state additive manufacturing process to enable the repair of expensive turbine runners, critical to the power generation of hydroelectric plants. Our solution enables stronger, longer lasting repairs, and minimizes the cost of maintenance when compared to the requirements for conventional fusion-based welding.”
Team captain, Joey Griffiths, explained, “Our team’s submission focused around using solid-state additive manufacturing to repair and reinforce metal turbine runners.” The technique, developed by Virginia Tech scientists and commercialized locally by the MELD Manufacturing Corporation in Christiansburg, involves “heating material through friction and deformation, enabling 3D printing of metals without melting. This enables the combination of more varied alloys and reduces the residual stress that can be caused by replacing large sections of material.”
A major innovation introduced by the team was the underwater application of their technique using a custom-designed and built enclosure to deposit stainless steel. Implementation of this process at a hydroelectric plant would allow for turbine repair without dewatering (draining and drying) of the plant, thereby improving efficiency and offering extensive savings in the repair of turbines.
Eleven submissions out of the 42 were selected for the top awards of Innovator and Grand prizes. Ten teams, including MSE-VT, received the Innovator Prize of $15,000.
Fusion-Free Fabrication team members include Joey Griffiths, Captain, Mackenzie Perry, David Garcia, W. Douglas Hartley, and faculty sponsor, Hang Yu - faculty
Check out the team’s prize-winning video here: https://www.youtube.com/watch?v=MZ1OX7dpXow&t=3s